G'Day Alan.
I have a library article on Chevrons which has
some of the same techniques for this blank construction. I'll add some pictures below that I have posted before, but am not positive they are still accessible; if not they may be in the future. Truly, ask me any questions - as I have stated, seeing how this is done is only the start, you will need to tweak your process and may come up with a better one. And the best result of getting a head start on some designs... You'll come up with your own that are different.
After the new IAP Site settles down and the Library is open for new articles I intend to write several articles.
However, to answer your question, I cut 45 degree slices from the initial "brick" - pen blank size for these actually. Then I simply used a disk sander to get the ends that were in the middle joints of the cross to be even in their color pattern. This was easy. The amount of the spectraply sticking out is easily trimed/sanded. I have one picture where there seems considerable waste, but as
it was only about 1/4" I was not concerned.
I used a table-top model-makers table saw (Byrnes), but have also previously used by large Craftsman Table saw with a 45 degree angle sled.
Time... These blanks took me in cumulative time less than 2 hrs. I would cut the slices, sand then even, cut the walnut cross pieces, glue the pattern together and let dry for 1-2 hrs (Tightbond Translucent, but I suspect other wood glues are fine). Then I added the black veneers and side pieces. Marked the ends CAREFULLY between the pattern, turned round, placed in a collet chuck to drill the tube hole. The glue onto the tube with more veneers and end caps (2 part epoxy for wood to tube).
Honestly, this pen looks a bit daunting if you have not done much segmenting, but is is a very reasonable blank to start with. Very worth the time. It is a nice project to do while doing other projects as you need to wait for the glue to dry fully.
I made the first pen with Olivewood and a thin cross. While it looks OK, I tweaked it to make the cross look "closer" e.g., wider segments, and used Cedar from Lebanon instead of the Olivewood. I felt the Olivewood distracted from the segmenting, and the Cedar of Lebanon was equally appropriate for the theme.
Hope this is helpful, and ask any questions if any arise. And do make this yourself, lots of fun when they work!
Cheers, Mark
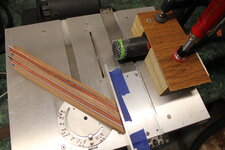
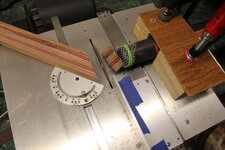
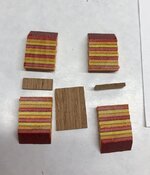
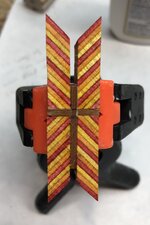
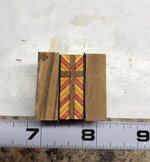