In all my hobbies, I frequently find that when I get deeper down the rabbit hole to the point of having questions about really specific minutiae, internet forums are full of opinions (even contradictory opinions), and there comes a point where online research will only take you so far.
To that end I'm trying things out myself so I can see results in person side-by-side and form my own preferences.
That said, there's a wealth of knowledge and experience here, so I figure I'll have plenty of questions to ask along the way.
When I first started woodturning nearly 20 years ago, it was in a Jr. High shop class. The teacher showed us the basics of how to use spindle gouges, explained the way sandpaper is supposed to be used in successively finer grits, and demonstrated exactly one finish: friction polish. Makes perfect sense in hindsight. It's inexpensive, relatively easy to apply, and makes for a pretty impressive glossy outcome in short order.
I finished many pens by sanding from 180 to 600 or 800 grit (often poorly), and then hitting with a single coat of friction polish. Throw the lathe speed up to max, squirt a little on a cotton rag, and rub it on until my fingers burned and the pen looked shiny. This was, I have to assume, a shellac-based friction polish. The pens always looked awesome until about the time I was done assembling them, at which point they had dulled noticeably, and by the end of the first sentence written, they looked fairly... bad.
Years later after I finished high school, I did some reading in search of polish that would stay nice-looking for longer, and of course quickly found CA finishing to be the de-facto standard for an incredibly durable, high-gloss pen finish. Since then, I have gotten results I'm fairly happy with (though I'm finding the skill ceiling on going from "great" to "perfect" with CA finish is very high, and constantly working to improve my technique). I will generally pop the grain with some BLO, burnish it off at a high speed to help fast track the curing and remove excess, and then put in 6-8 coats of medium CA, leveling with 600 grit wet paper, and polishing from there with wet micromesh/Novus #2, or more recently, Dr. Kirk's micro magic waxes, which seem to produce identical results with less effort and fuss than micromesh pads.
Lately I've been reading about different options. Aside from just being kinda time consuming, inconvenient (needing nonstick bushings, accidentally sanding through the glue, etc. etc.) and rather prone to errors that show up as obvious imperfections in the final glossy coat, I was encouraged after reading Phil Dart's article on melamine lacquer finish with a pure carnauba wax top coat to protect from fingerprints and give the lacquer time to fully cure.
The idea of having a very high-gloss, durable pen finish that gives a slightly more natural "wood" feel to the pen than the notably plastick-y CA glue was very appealing, and seemed like a worthwhile option to add to my arsenal.
Unfortunately I can't seem to source melamine lacquer easily or inexpensively. Beaufort Inks won't ship it to the US, and everywhere else wants to sell me 3 cans, each costing $30. A lot to spend on an experiment that may or may not bear out.
Some additional reading suggested that nitrocellulose lacquer might work very similarly. A few other people had suggested a DIY friction polish that seemed like essentially the same thing, and importantly, consisted of ingredients I already had on hand. Equal parts by volume of Deft gloss brush-on lacquer, lacquer thinner, and BLO. Cool. Applied more or less the same as my old shellac-based friction polish: wipe it on, spin it fast, and let the pressure/heat from the shop towel evaporate the solvents and cure the lacquer quickly. Apparently one can build up several coats in short order and achieve an excellent gloss that nevertheless feels a bit more natural than CA finish.
I turned a quick slimline today to try it out. Sanded up through 600 grit, cleaned quickly with acetone, and gave it a shot. I did 6 coats on this pen, and got it hot enough with each coat that it was actually smoking a bit. On the lathe it appeared to be building a really solid gloss, and application was indeed as easy as I remember from my shellac friction polish days. It was dry to the touch between each application. I finished with a bit of renaissance wax over the top (I do that on all my pens to help prevent fingerprints).
And... once again, by the time I got it assembled and started writing with it, it was disappointingly dull.
Here is a photo showing a walnut slimline I CA finished a couple of days ago on the left, and a walnut slimline I finished today with this lacquer-based friction polish on the right. The lacquer pen obviously looks more like wood, as it should. But it's a dreadful finish compared to the CA, for someone who wanted high gloss and durability. (Click thumbnail for expanded view) It's downright matte next to the CA finish.
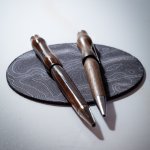
So my questions, in no particular order, are:
1. Would this be significantly improved by using a cellulose sealer prior to the lacquer-based friction polish? Walnut is fairly porous.
2. Would this be significantly improved by building more than 6 coats?
3. Is there something wrong with my application technique that is hurting the gloss or durability of my finish?
4. Is this something that's really only going to work well with melamine lacquer as opposed to nitrocellulose?
5. What other suggestions do you have for a newbie looking to achieve a finish that checks all the boxes (easy to apply on the lathe, low-mess, no long cure times needed, high gloss, durable, less plastick-y feeling than CA)?
To that end I'm trying things out myself so I can see results in person side-by-side and form my own preferences.
That said, there's a wealth of knowledge and experience here, so I figure I'll have plenty of questions to ask along the way.
When I first started woodturning nearly 20 years ago, it was in a Jr. High shop class. The teacher showed us the basics of how to use spindle gouges, explained the way sandpaper is supposed to be used in successively finer grits, and demonstrated exactly one finish: friction polish. Makes perfect sense in hindsight. It's inexpensive, relatively easy to apply, and makes for a pretty impressive glossy outcome in short order.
I finished many pens by sanding from 180 to 600 or 800 grit (often poorly), and then hitting with a single coat of friction polish. Throw the lathe speed up to max, squirt a little on a cotton rag, and rub it on until my fingers burned and the pen looked shiny. This was, I have to assume, a shellac-based friction polish. The pens always looked awesome until about the time I was done assembling them, at which point they had dulled noticeably, and by the end of the first sentence written, they looked fairly... bad.
Years later after I finished high school, I did some reading in search of polish that would stay nice-looking for longer, and of course quickly found CA finishing to be the de-facto standard for an incredibly durable, high-gloss pen finish. Since then, I have gotten results I'm fairly happy with (though I'm finding the skill ceiling on going from "great" to "perfect" with CA finish is very high, and constantly working to improve my technique). I will generally pop the grain with some BLO, burnish it off at a high speed to help fast track the curing and remove excess, and then put in 6-8 coats of medium CA, leveling with 600 grit wet paper, and polishing from there with wet micromesh/Novus #2, or more recently, Dr. Kirk's micro magic waxes, which seem to produce identical results with less effort and fuss than micromesh pads.
Lately I've been reading about different options. Aside from just being kinda time consuming, inconvenient (needing nonstick bushings, accidentally sanding through the glue, etc. etc.) and rather prone to errors that show up as obvious imperfections in the final glossy coat, I was encouraged after reading Phil Dart's article on melamine lacquer finish with a pure carnauba wax top coat to protect from fingerprints and give the lacquer time to fully cure.
The idea of having a very high-gloss, durable pen finish that gives a slightly more natural "wood" feel to the pen than the notably plastick-y CA glue was very appealing, and seemed like a worthwhile option to add to my arsenal.
Unfortunately I can't seem to source melamine lacquer easily or inexpensively. Beaufort Inks won't ship it to the US, and everywhere else wants to sell me 3 cans, each costing $30. A lot to spend on an experiment that may or may not bear out.
Some additional reading suggested that nitrocellulose lacquer might work very similarly. A few other people had suggested a DIY friction polish that seemed like essentially the same thing, and importantly, consisted of ingredients I already had on hand. Equal parts by volume of Deft gloss brush-on lacquer, lacquer thinner, and BLO. Cool. Applied more or less the same as my old shellac-based friction polish: wipe it on, spin it fast, and let the pressure/heat from the shop towel evaporate the solvents and cure the lacquer quickly. Apparently one can build up several coats in short order and achieve an excellent gloss that nevertheless feels a bit more natural than CA finish.
I turned a quick slimline today to try it out. Sanded up through 600 grit, cleaned quickly with acetone, and gave it a shot. I did 6 coats on this pen, and got it hot enough with each coat that it was actually smoking a bit. On the lathe it appeared to be building a really solid gloss, and application was indeed as easy as I remember from my shellac friction polish days. It was dry to the touch between each application. I finished with a bit of renaissance wax over the top (I do that on all my pens to help prevent fingerprints).
And... once again, by the time I got it assembled and started writing with it, it was disappointingly dull.
Here is a photo showing a walnut slimline I CA finished a couple of days ago on the left, and a walnut slimline I finished today with this lacquer-based friction polish on the right. The lacquer pen obviously looks more like wood, as it should. But it's a dreadful finish compared to the CA, for someone who wanted high gloss and durability. (Click thumbnail for expanded view) It's downright matte next to the CA finish.
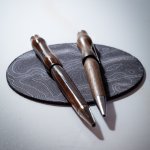
So my questions, in no particular order, are:
1. Would this be significantly improved by using a cellulose sealer prior to the lacquer-based friction polish? Walnut is fairly porous.
2. Would this be significantly improved by building more than 6 coats?
3. Is there something wrong with my application technique that is hurting the gloss or durability of my finish?
4. Is this something that's really only going to work well with melamine lacquer as opposed to nitrocellulose?
5. What other suggestions do you have for a newbie looking to achieve a finish that checks all the boxes (easy to apply on the lathe, low-mess, no long cure times needed, high gloss, durable, less plastick-y feeling than CA)?