sorcerertd
Member
My question applies to more than just the whiskey barrel staves, but it's the most unstable type of material that I want to work with at the moment. The pen below was made with a stave from Maker's Mark. There are two things that I'm seeking advise with here.
I do also have a stadium seat blank that I'd like to drill the same way to retain some of the paint. At least the seat is curved more sharply to make it more doable, but I still have to drill the walls quite thin! Also, the stadium blank cost enough that I really don't want to mess it up. I've watched a couple Youtube videos and they don't address stabilizing or supporting the thin walled side. I'd rather not make a really bulbous pen if I can avoid it.
* On an unrelated note: I had the idea that making a barrel style mini pepper mill from some staves would be pretty cool. I doubt that the charring would flavor the pepper much, but the idea is intriguing.
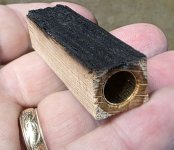
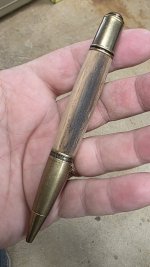
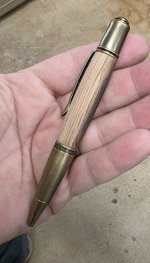
- Stabilizing - The finished barrel didn't retain the texture I was looking for. In fact, I scored it with some 40 grit after turning it just to put some texture back in it. Here's what I did with the blank:
a. "Stabilized" the charred side with thin CA.
b. Put a thin strip of wood against the charred side to offset the hole while drilling. It was not glued to the side of the blank because I didn't want to have to remove it without damaging the focal point, but held firmly in place by the pen jaws.
- Drilling - Even with the stabilization, it cracked a little with the wall being so thin, and I still was left with less of the char than I wanted.
As far as the crack, the glue bond between the tube and wood held it together, but I really would like to drill it so that the wall is thinner on the charred side. It's obviously much more likely to crack that way. I even used a monarch grande instead of a regular sized sierra style so the barrel would have more thickness to it.
I do also have a stadium seat blank that I'd like to drill the same way to retain some of the paint. At least the seat is curved more sharply to make it more doable, but I still have to drill the walls quite thin! Also, the stadium blank cost enough that I really don't want to mess it up. I've watched a couple Youtube videos and they don't address stabilizing or supporting the thin walled side. I'd rather not make a really bulbous pen if I can avoid it.
* On an unrelated note: I had the idea that making a barrel style mini pepper mill from some staves would be pretty cool. I doubt that the charring would flavor the pepper much, but the idea is intriguing.
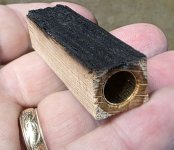
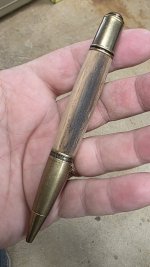
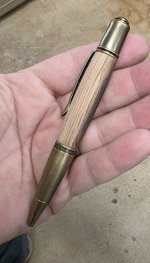