Dan_F
Member
Getting my skew chisel "shaving sharp" was driving me batty, until I made this wheel for my lathe. My grinder would leave a burr after grinding, and I had tried numerous methods to do the final honing, with generally inconsistent results. I found it very difficult to put a consistent edge on my curved skews.
This has made a big difference in the quality of edge I can now obtain. It's made from 2 pieces of mdf, 3/4" for the larger wheel, 1/2" for the smaller.
The second, smaller wheel is glued and screwed to the larger one, partly to give added support, but mainly to act as a spacer that allows the treads to stay positioned where they will be engaged, and also but up against the face of the spindle.
The larger of the two is just under 8" diameter, to match my grinder, and has a center hole bored, then tapped with a Beall Spindle Tap, http://www.woodcraft.com/family.aspx?familyid=20109
to match the threads on my spindle. I dosed the newly cut threads liberally with a few coats of thin CA glue to toughen them up, and they are holding up well.
The wheels were cut on the band saw, and trued up on the lathe with a scraper. I applied 2000 grit sandpaper to the exposed face of the wheel, but soon found that green buffing compound applied to the edge worked much better. I use the tool rest for, well, resting the tool when honing, which makes the whole process much more precise than trying to freehand.
The downside to this setup is that I have to remove the wheel when turning, as it takes up some space, and I don't know how well MDF holds together at 3200 RPM's, and don't want to learn the hard way.
The other thing to remember is to put the lathe in reverse, or else hone from behind the lathe, as the honing action has the wheel going away from the blade, rather than toward is as when grinding.
I can now get razor sharp cutting edges on my skews, and can renew them a time or two before going back to the grinder. It makes a big difference when working with burls especially, which will tend to tear out with anything less than razor sharp tools. It does the same thing as the leather wheel on a Tormek, but costs a LOT less, and takes up less space.
Dan
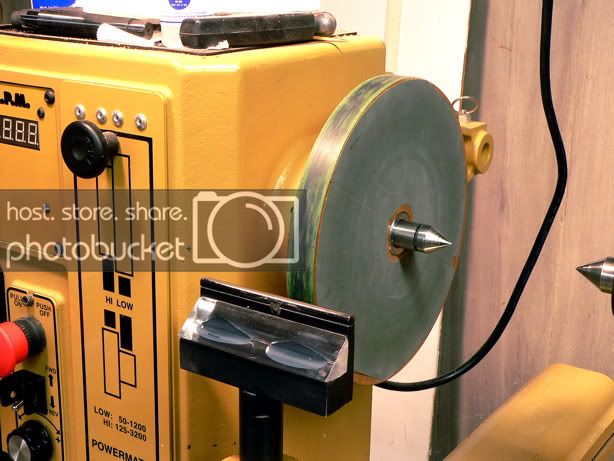
This has made a big difference in the quality of edge I can now obtain. It's made from 2 pieces of mdf, 3/4" for the larger wheel, 1/2" for the smaller.
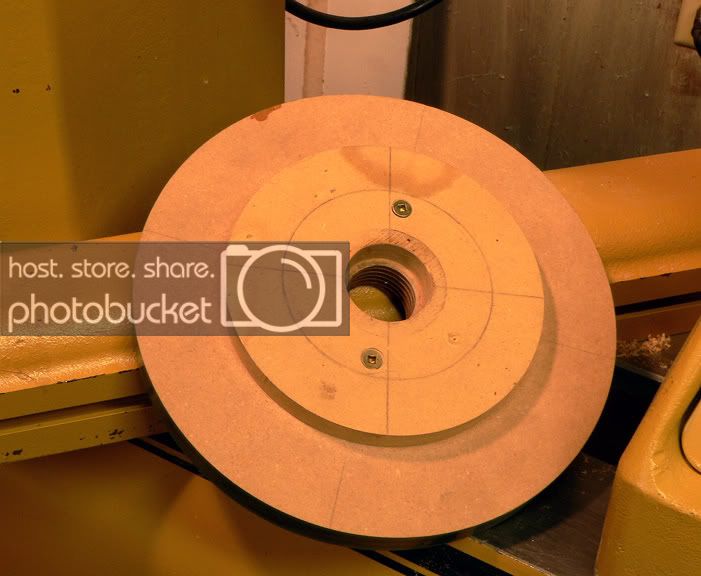
The second, smaller wheel is glued and screwed to the larger one, partly to give added support, but mainly to act as a spacer that allows the treads to stay positioned where they will be engaged, and also but up against the face of the spindle.
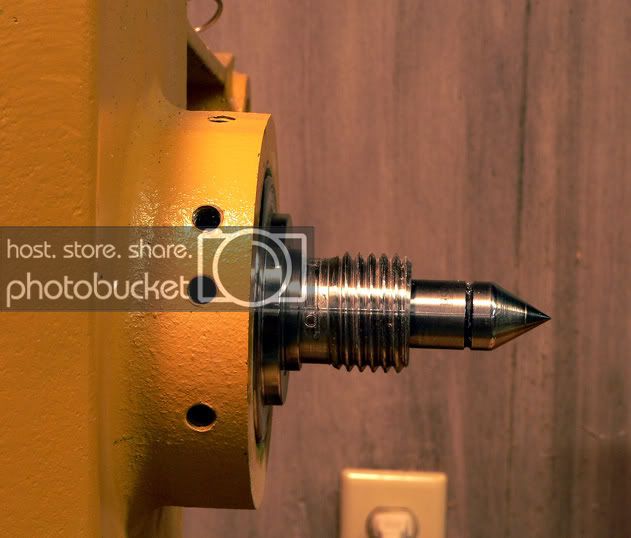
The larger of the two is just under 8" diameter, to match my grinder, and has a center hole bored, then tapped with a Beall Spindle Tap, http://www.woodcraft.com/family.aspx?familyid=20109
to match the threads on my spindle. I dosed the newly cut threads liberally with a few coats of thin CA glue to toughen them up, and they are holding up well.
The wheels were cut on the band saw, and trued up on the lathe with a scraper. I applied 2000 grit sandpaper to the exposed face of the wheel, but soon found that green buffing compound applied to the edge worked much better. I use the tool rest for, well, resting the tool when honing, which makes the whole process much more precise than trying to freehand.
The downside to this setup is that I have to remove the wheel when turning, as it takes up some space, and I don't know how well MDF holds together at 3200 RPM's, and don't want to learn the hard way.
The other thing to remember is to put the lathe in reverse, or else hone from behind the lathe, as the honing action has the wheel going away from the blade, rather than toward is as when grinding.
I can now get razor sharp cutting edges on my skews, and can renew them a time or two before going back to the grinder. It makes a big difference when working with burls especially, which will tend to tear out with anything less than razor sharp tools. It does the same thing as the leather wheel on a Tormek, but costs a LOT less, and takes up less space.
Dan