Dana Fish
Member
Hello all.....
I have recently started to practice turning pens on the lathe, it fun and all but my frustration comes in when I get to the near end of the finishing the turning process and I blow out a chuck off the end off the blank. I have posted pics below of my situation this morning in hopes that someone may have an idea how to prevent this from happen in the future.
I question if I am using enough glue? Are my tools sharp enough? Or do I just have that much bad luck that I keep choosing weak blanks?
Any advice or pointers would be greatly appreciated.
I have recently started to practice turning pens on the lathe, it fun and all but my frustration comes in when I get to the near end of the finishing the turning process and I blow out a chuck off the end off the blank. I have posted pics below of my situation this morning in hopes that someone may have an idea how to prevent this from happen in the future.
I question if I am using enough glue? Are my tools sharp enough? Or do I just have that much bad luck that I keep choosing weak blanks?
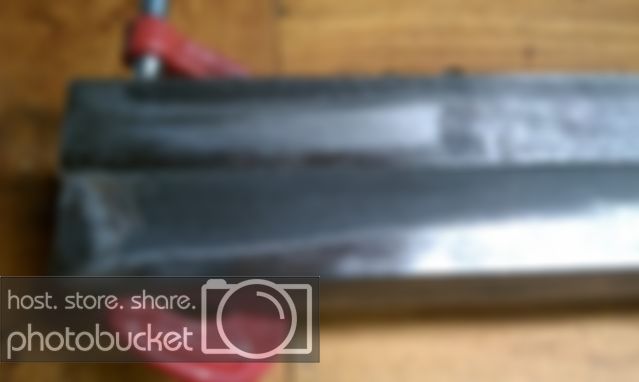
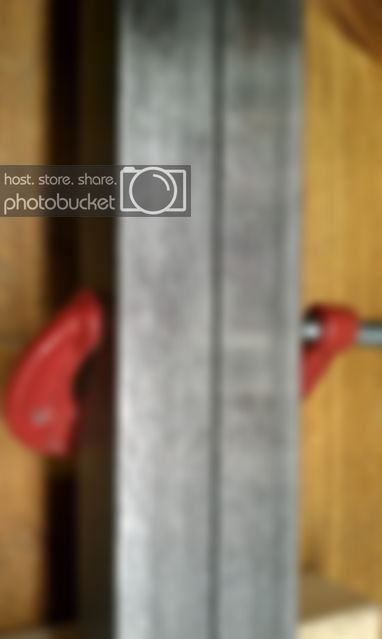
Any advice or pointers would be greatly appreciated.