Frankly, I have no idea about kit pens. Never considered making one or even buying one.
What happened was, I got frustrated with the sort of pens I could afford. Grew queasy at the waste implied in cartridges. The converters are too small. Ok, the Twisby vacuum filler is big enough, but has sharp threads and shoulders right in the middle of my grip. I despair of finding a decent vintage wet noodle at an affordable (to me) price, and one wet noodle isn't enough : you need one for every colour, don't you?
The only way was to design a better pen myself. For simplicity's sake, I started with the idea of Noodlers' piston filler : a simple syringe with a hollow piston, a little air-tube in the back of the feed, just long enough to clear the end of the piston when pressed down all the way. It creates enough of a vacuum to almost entirely fill the pen.
Dad taught me to keep my fingers high on the pen : when your fingers are higher, you need less movement to cover a larger surface. It had to be a pen with a smooth section.
I spent a month or two drawing up plans, then bought a lathe and started building. Five parts to build, four to buy. The section and the reservoir are one piece; the piston is hollow, has a foot with a groove for the o-ring and a ridged end to push and pull; the hollow bolt to retain the piston in the reservoir screws into the end of the reservoir; the back cap slips over the piston and screws onto the body, and the top cap has an inside cone that is hardly wider than the cone of the section. When closed, the cap and pen form a thin watertight join at the top of the pen, which is easy to pop open, and closes securely, with no fear of leakage outside the cap.
Ergonomically it works exactly to requirements : it is a pleasure to use. But it is a bear to build.
For one, my tools are limited. I have a mini-lathe from the empire on the other side, with semi permanent analog read-outs, a gear box that has to be unbuilt to change gears, and a tail-stock that is a hundredth of a mm or so too high. And I haven't the wherewithal to scrape it down. I pee with the willie i got.
It gets worse. Acrylic turns ok, but it isn't easy. It starts to melt close to the boiling point of water (see what I did there? No celsius, no farenheit!). A 1/10" drill bit will start to boil the material about 1/2" in, at 175 rpm. I had to develop a ritual : drill 10 mm deep, change to a drill 1/2 mm smaller, drill another 10 mm, rinse and repeat, to size. Finish with a boring bar for a straight hole. Well, straight-ish. The plastic bends under tool pressure. The beginning of a bore is always tighter than the end, the beginning of an outside cut is always wider than near the chuck. Which leaves one with the unthankful task of keeping both ends within tolerance.
The design of the pen leaves but little material for the hollow bolt : I didn't want the pen to be wider than a Montblanc, which is 16mm at its widest, and I wanted a reservoir of at least 10mm diameter, so it could accommodate a hollow piston. All these parts screw together over the same length in the middle of the pen. I decided to give the most wall thickness to the outside, and the least to the hollow bolt : it only has to stop the piston from slipping out, and rarely needs to be manipulated.
I chose triple entry thread. That is to say, I would have tried quadruple entry, but my gearbox isn't big enough to accept the gears for that. As it is, at a speed of 3mm per revolution, I am already over the nominal maximum of the machine. Doesn't matter, I have to turn the threads by hand anyway. You know the procedure : turn one thread to size, advance the tool 1 mm on the compound slide, turn the second, repeat for the third. test for fit and cut a little deeper if required. For the flange on the body that takes both inside and outside threads, I try to position them so that the valleys on one side fall on the ridges of the other, to keep the maximum possible wall thickness.
All of this makes for a pen that costs a lot of time to make, with a result that can never be as polished as it should be. There is no way I could make the bore of the piston perfectly straight and polished : the hole is only 5,5 mm, and the drill bit will weave about the center to leave me with a helicoidal deformation of the bore. However much care I take with the bore of the reservoir, I need to hedge with two sizes of o-ring, and possible adjustments to the o-ring groove. No matter how precisely I try to replicate each cutting procedure, I can make each pen fit with itself, but the pieces are hardly interchangeable.
Here it is, my stupidly good pen that I cannot make good enough to sell :
If you're interested, I'll happily share the plans.
I would dearly love to see my design sold cheap in retail, but I doubt it can be done. Making moulds for the pieces is non-trivial, what with inside and outside shoulders and threads with clearances required - it boggles the mind. CNC machining is feasible, but again, I dont think they could be produced in large enough numbers to be able to sell them at a reasonable price.
If any of you have ideas or suggestions, please go ahead. Anything to minimise the pain of making them and maximise the pleasure of using them.
Cheers.
bonus : here is one fitted with a Zebra G chrome-plated nib. Works beautifully with Noodlers black, Apache Sunset, Saguaro Wine and Nikita Red. Diamine Blue-black will eat the nib.
What happened was, I got frustrated with the sort of pens I could afford. Grew queasy at the waste implied in cartridges. The converters are too small. Ok, the Twisby vacuum filler is big enough, but has sharp threads and shoulders right in the middle of my grip. I despair of finding a decent vintage wet noodle at an affordable (to me) price, and one wet noodle isn't enough : you need one for every colour, don't you?
The only way was to design a better pen myself. For simplicity's sake, I started with the idea of Noodlers' piston filler : a simple syringe with a hollow piston, a little air-tube in the back of the feed, just long enough to clear the end of the piston when pressed down all the way. It creates enough of a vacuum to almost entirely fill the pen.
Dad taught me to keep my fingers high on the pen : when your fingers are higher, you need less movement to cover a larger surface. It had to be a pen with a smooth section.
I spent a month or two drawing up plans, then bought a lathe and started building. Five parts to build, four to buy. The section and the reservoir are one piece; the piston is hollow, has a foot with a groove for the o-ring and a ridged end to push and pull; the hollow bolt to retain the piston in the reservoir screws into the end of the reservoir; the back cap slips over the piston and screws onto the body, and the top cap has an inside cone that is hardly wider than the cone of the section. When closed, the cap and pen form a thin watertight join at the top of the pen, which is easy to pop open, and closes securely, with no fear of leakage outside the cap.
Ergonomically it works exactly to requirements : it is a pleasure to use. But it is a bear to build.
For one, my tools are limited. I have a mini-lathe from the empire on the other side, with semi permanent analog read-outs, a gear box that has to be unbuilt to change gears, and a tail-stock that is a hundredth of a mm or so too high. And I haven't the wherewithal to scrape it down. I pee with the willie i got.
It gets worse. Acrylic turns ok, but it isn't easy. It starts to melt close to the boiling point of water (see what I did there? No celsius, no farenheit!). A 1/10" drill bit will start to boil the material about 1/2" in, at 175 rpm. I had to develop a ritual : drill 10 mm deep, change to a drill 1/2 mm smaller, drill another 10 mm, rinse and repeat, to size. Finish with a boring bar for a straight hole. Well, straight-ish. The plastic bends under tool pressure. The beginning of a bore is always tighter than the end, the beginning of an outside cut is always wider than near the chuck. Which leaves one with the unthankful task of keeping both ends within tolerance.
The design of the pen leaves but little material for the hollow bolt : I didn't want the pen to be wider than a Montblanc, which is 16mm at its widest, and I wanted a reservoir of at least 10mm diameter, so it could accommodate a hollow piston. All these parts screw together over the same length in the middle of the pen. I decided to give the most wall thickness to the outside, and the least to the hollow bolt : it only has to stop the piston from slipping out, and rarely needs to be manipulated.
I chose triple entry thread. That is to say, I would have tried quadruple entry, but my gearbox isn't big enough to accept the gears for that. As it is, at a speed of 3mm per revolution, I am already over the nominal maximum of the machine. Doesn't matter, I have to turn the threads by hand anyway. You know the procedure : turn one thread to size, advance the tool 1 mm on the compound slide, turn the second, repeat for the third. test for fit and cut a little deeper if required. For the flange on the body that takes both inside and outside threads, I try to position them so that the valleys on one side fall on the ridges of the other, to keep the maximum possible wall thickness.
All of this makes for a pen that costs a lot of time to make, with a result that can never be as polished as it should be. There is no way I could make the bore of the piston perfectly straight and polished : the hole is only 5,5 mm, and the drill bit will weave about the center to leave me with a helicoidal deformation of the bore. However much care I take with the bore of the reservoir, I need to hedge with two sizes of o-ring, and possible adjustments to the o-ring groove. No matter how precisely I try to replicate each cutting procedure, I can make each pen fit with itself, but the pieces are hardly interchangeable.
Here it is, my stupidly good pen that I cannot make good enough to sell :
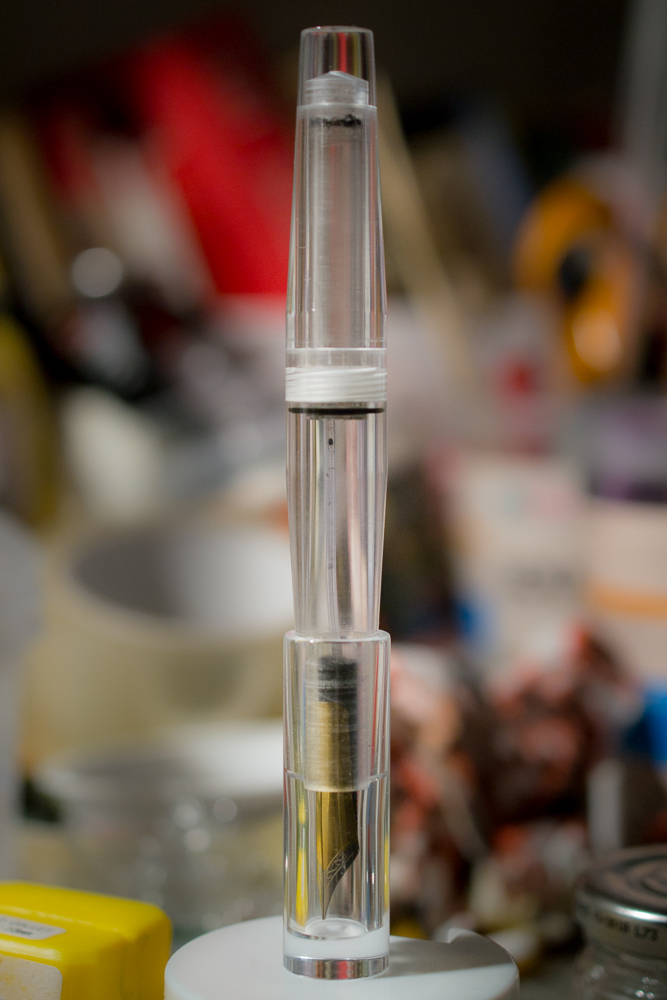
If you're interested, I'll happily share the plans.
I would dearly love to see my design sold cheap in retail, but I doubt it can be done. Making moulds for the pieces is non-trivial, what with inside and outside shoulders and threads with clearances required - it boggles the mind. CNC machining is feasible, but again, I dont think they could be produced in large enough numbers to be able to sell them at a reasonable price.
If any of you have ideas or suggestions, please go ahead. Anything to minimise the pain of making them and maximise the pleasure of using them.
Cheers.
bonus : here is one fitted with a Zebra G chrome-plated nib. Works beautifully with Noodlers black, Apache Sunset, Saguaro Wine and Nikita Red. Diamine Blue-black will eat the nib.
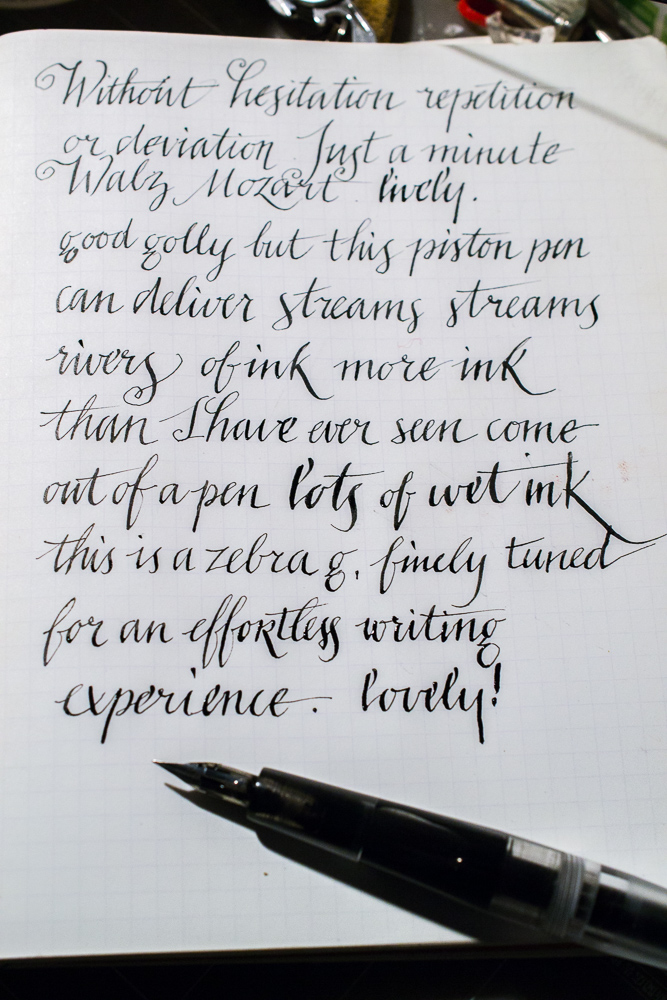