Although I have been remiss about posting photos of my work, I thoroughly enjoy this hobby and participating on this great website. . I have made some great friends who have shared all I have requested and more. . Without their kindness I would still be in the backwaters. . With their help I have been able to advance my skills to a point where I get great satisfaction out of making pens, pens, and more pens !
Some of you may have missed my entry in this year's BASH Kitless Contest. . Some of you may have recognized my work. . Some of you, maybe not. . Some of you may recognize your influence on this work even if you were unable to identify it as "my" work. . Thank you to ALL ! . Your contributions to my enjoyment of the hobby are GREATLY APPRECIATED !! . Thanks again and again !
Anyway, for what it is worth - a gratifying Third Prize as it turned out - here it is for the record.
***** A Novel Kitless Ballpoint Pen Design *****
Nothing twisted about this one ... 5 straight bars of wood and 4 straight grooves, then glue and turning.
The center bar is hard maple and the others are Thuya Burl. All parts were made by me except the spring,
refill, and the internal click mechanism. All hardware is brass, shaped on my metal lathe and mill.
The pushbutton top is oversized and milled "square" so that it acts as a roll stop. No clip as this is
intended to be a desktop pen. The red ends on the barrel are dyed and stabilized maple burl. CA finish.
The large pushbutton is machined with conical top and bottom surfaces; squared edges appear "elliptical".
One picture shows the refill retracted; one picture extended; both pics show pushbutton in normal position.
The third picture shows the pushbutton held in the pushed down position; refill is extended beyond normal.
In the down position, the button lower cone fits in a concave depression machined in the pen's top finial.


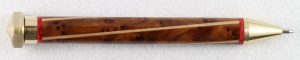
Some of you may have missed my entry in this year's BASH Kitless Contest. . Some of you may have recognized my work. . Some of you, maybe not. . Some of you may recognize your influence on this work even if you were unable to identify it as "my" work. . Thank you to ALL ! . Your contributions to my enjoyment of the hobby are GREATLY APPRECIATED !! . Thanks again and again !
Anyway, for what it is worth - a gratifying Third Prize as it turned out - here it is for the record.
***** A Novel Kitless Ballpoint Pen Design *****
Nothing twisted about this one ... 5 straight bars of wood and 4 straight grooves, then glue and turning.
The center bar is hard maple and the others are Thuya Burl. All parts were made by me except the spring,
refill, and the internal click mechanism. All hardware is brass, shaped on my metal lathe and mill.
The pushbutton top is oversized and milled "square" so that it acts as a roll stop. No clip as this is
intended to be a desktop pen. The red ends on the barrel are dyed and stabilized maple burl. CA finish.
The large pushbutton is machined with conical top and bottom surfaces; squared edges appear "elliptical".
One picture shows the refill retracted; one picture extended; both pics show pushbutton in normal position.
The third picture shows the pushbutton held in the pushed down position; refill is extended beyond normal.
In the down position, the button lower cone fits in a concave depression machined in the pen's top finial.
Last edited: