Ed McDonnell
Member
Casting:
Forgot to take measurements before mailing, but it should be about 6" long and a little over 0.5" diameter. #5 bock nib and it's not intended to post. First cast was dark blue PR. Carved the design with my ornamental lathe and cast a second time with metal filled PR. Used aluminum and zinc to simulate pewter.
Open:
A celtic twist on the flag pen theme. Red, white and blue PR. Double casts.
Ed
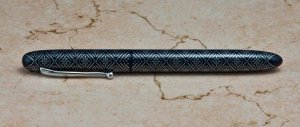

Forgot to take measurements before mailing, but it should be about 6" long and a little over 0.5" diameter. #5 bock nib and it's not intended to post. First cast was dark blue PR. Carved the design with my ornamental lathe and cast a second time with metal filled PR. Used aluminum and zinc to simulate pewter.
Open:
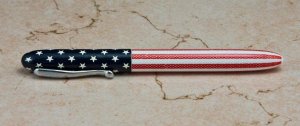
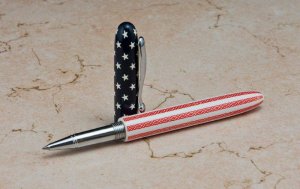
A celtic twist on the flag pen theme. Red, white and blue PR. Double casts.
Ed