W.Y.
Member
Not sure if this is the right board to post this in this site. If not, perhaps one of the mods will be so kind as to re-direct it to the most appropriate one.
I put this topic on the Segmented Turning board of my own Woodworking Friends site because black as well as white and colored veneers are used extensively in making segmented bowls and vessels.
I decided to share it here as well for the benefit of anyone that might be interested because wood veneer is also used by some in pen making and for some it is favored over using colored plastic veneers.
I have gathered various sources of information on how to dye veneer black so decided to try this particular method.
Why ? because it doesn't cost much and uses ingredients readily available . .
Apparently darker wood like walnut and oak with its tannin content works better in combination with the steel wool and vinegar solution so we will see how this goes with cherry and birch. These are the only two species of veneer I had to work with .
Here are the ingredients to start with.
To one quart of cider vinegar add one pad of steel wool . First wash the steel wool in warm soapy water because it contains oils to prevent rusting. . Rinse and dry either in the sun or in a regular warm oven on an aluminum pie plate. DO NOT use microwave oven for this. If rust forms when drying in the sun , it is not a problem.
Here is the steel wool in the vinegar right at the start. It should be left like that for several days or even weeks. Extra time will not matter.
Steel wool totally dissolved in one week.
Four pieces of veneer cut . two cherry and two birch.
Soaking in solution with paper towel on bottom and between each piece and on top.
Covered with lid and waiting for complete saturation.
After one day soak I removed veneer from liquid and put it between two pieces of plywood with a sheet of paper towel above and below and between every piece of veneer. Clamped it down tight and set aside to dry.
After a couple days of being clamped between plywood and layers of paper towel , here is the result .
.
I was curious to see if the dye was only on the surface or all the way through so I cut a corner off and took a photo of the edge. Although it was difficult to get a good edge photo, it is apparent that the dye did go all the way through .
Conclusion.
Apparently woods with tannin content respond best to this method . The birch veneer obviously has low tannin content so didn't go black like the cherry veneer did under the same circumstances. . Walnut veneer is apparently a better choice than cherry but I did not have any to try.
It has been said that strong tea added to the vinegar and steel wool helps some because of its strong tannin content but I did not try that . I probably will the next time.
Next experiment whenever I get time will be with Rit dyes with DNA to get more colors of pieces than plain black.
Have never tried aniline dyes but they are supposed to be very good. Just don't want to tie up the money of having to buy them on line and pay S/H etc. until I hear and see proof that it is the best way to go. .
Sure, I know colored veneer is available on line but I enjoy doing stuff like this myself if it is at all practical . It is the price per square foot of pre-made ones verses shop made ones that must be figured in.
I put this topic on the Segmented Turning board of my own Woodworking Friends site because black as well as white and colored veneers are used extensively in making segmented bowls and vessels.
I decided to share it here as well for the benefit of anyone that might be interested because wood veneer is also used by some in pen making and for some it is favored over using colored plastic veneers.
I have gathered various sources of information on how to dye veneer black so decided to try this particular method.
Why ? because it doesn't cost much and uses ingredients readily available . .
Apparently darker wood like walnut and oak with its tannin content works better in combination with the steel wool and vinegar solution so we will see how this goes with cherry and birch. These are the only two species of veneer I had to work with .
Here are the ingredients to start with.
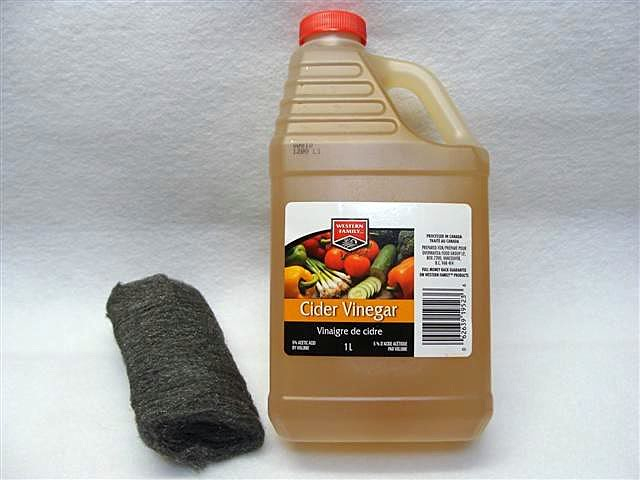
To one quart of cider vinegar add one pad of steel wool . First wash the steel wool in warm soapy water because it contains oils to prevent rusting. . Rinse and dry either in the sun or in a regular warm oven on an aluminum pie plate. DO NOT use microwave oven for this. If rust forms when drying in the sun , it is not a problem.
Here is the steel wool in the vinegar right at the start. It should be left like that for several days or even weeks. Extra time will not matter.
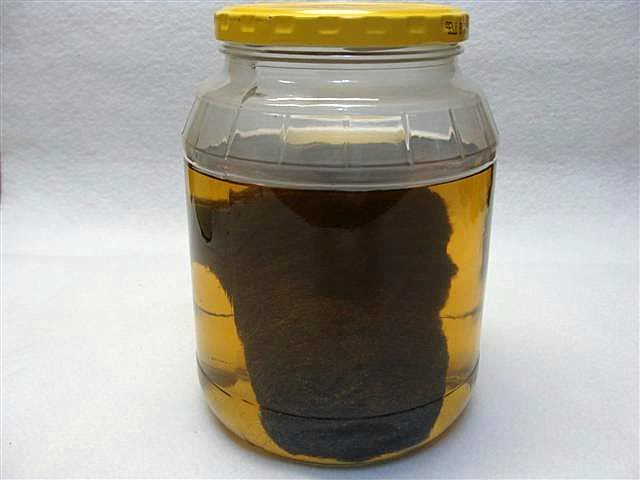
Steel wool totally dissolved in one week.
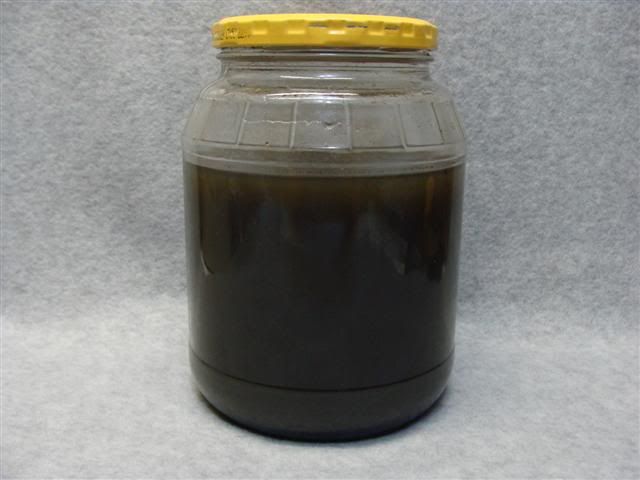
Four pieces of veneer cut . two cherry and two birch.

Soaking in solution with paper towel on bottom and between each piece and on top.
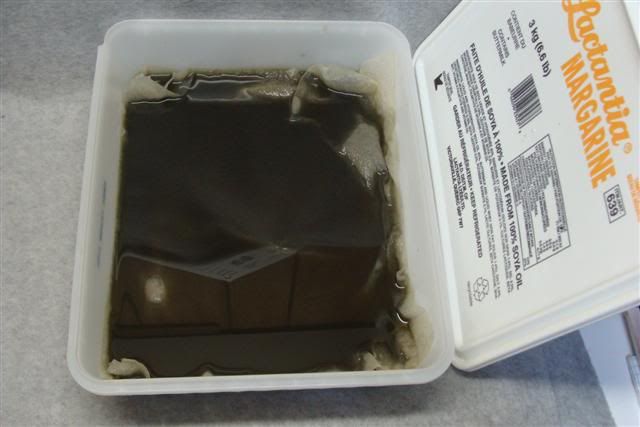
Covered with lid and waiting for complete saturation.
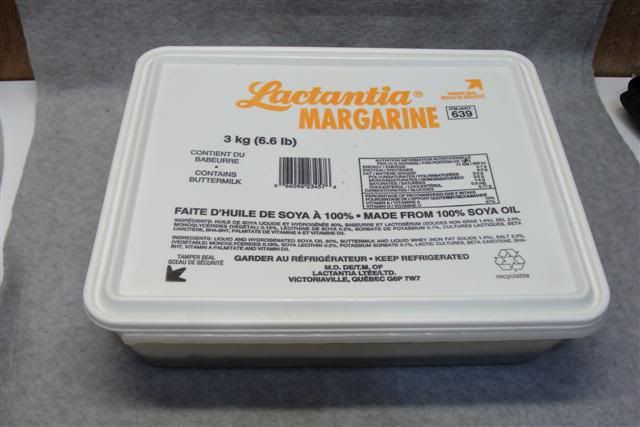
After one day soak I removed veneer from liquid and put it between two pieces of plywood with a sheet of paper towel above and below and between every piece of veneer. Clamped it down tight and set aside to dry.
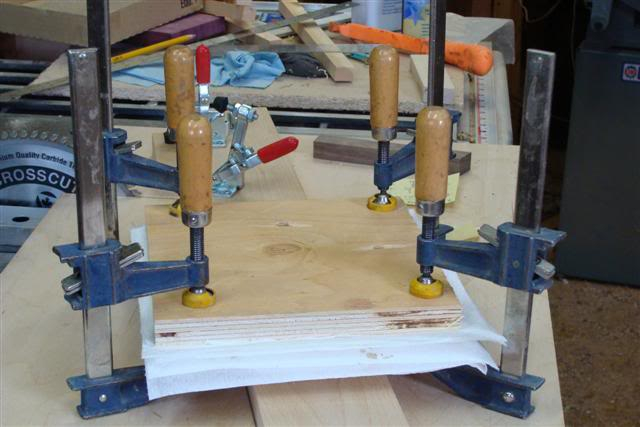
After a couple days of being clamped between plywood and layers of paper towel , here is the result .
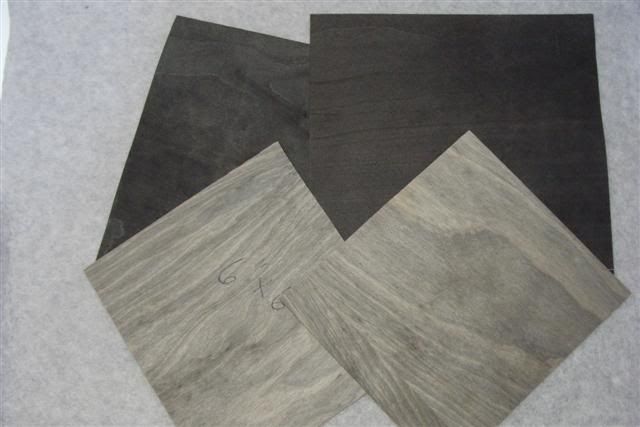
I was curious to see if the dye was only on the surface or all the way through so I cut a corner off and took a photo of the edge. Although it was difficult to get a good edge photo, it is apparent that the dye did go all the way through .
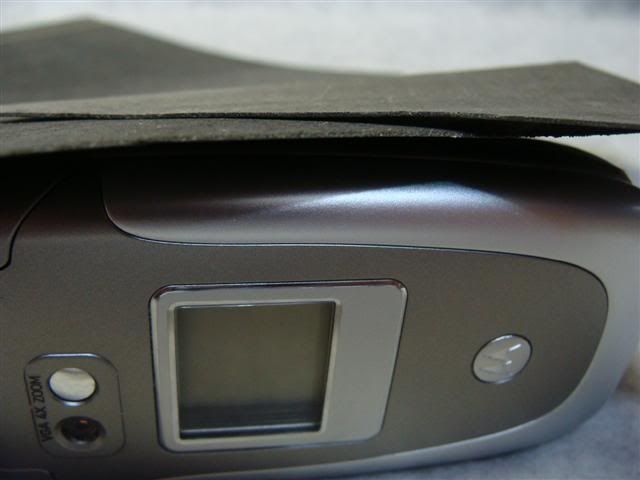
Conclusion.
Apparently woods with tannin content respond best to this method . The birch veneer obviously has low tannin content so didn't go black like the cherry veneer did under the same circumstances. . Walnut veneer is apparently a better choice than cherry but I did not have any to try.
It has been said that strong tea added to the vinegar and steel wool helps some because of its strong tannin content but I did not try that . I probably will the next time.
Next experiment whenever I get time will be with Rit dyes with DNA to get more colors of pieces than plain black.
Have never tried aniline dyes but they are supposed to be very good. Just don't want to tie up the money of having to buy them on line and pay S/H etc. until I hear and see proof that it is the best way to go. .
Sure, I know colored veneer is available on line but I enjoy doing stuff like this myself if it is at all practical . It is the price per square foot of pre-made ones verses shop made ones that must be figured in.