Triple Crown
Member
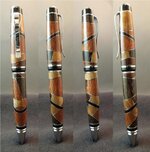
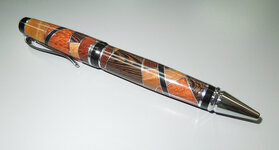
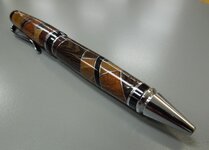
First of all, I'd really like to thank Landon (hunter-27) for organizing such a great event and the great people of IAP that make it so fun to be a part of the PITH exchange. I've loved reading everyone's posts and looking at the pictures of the pens that people have challenged themselves to make for their fellow penturners! I am really happy that I was matched with my new really good friend Russ (Russknan). We have exchanged a lot of e-mail and spurred each other on with 'teaser pics' and stories of our works-in-progress. We also found out that we have a lot in common with each other in our lives in general.
This pen took me a very very long time to make. I had an idea from the beginning of what I wanted it to look like, and I am pretty happy with the results. It is not 'perfect' and that is okay. It is my first wood segmented pen, and it is truly an IAP Pen! The different woods each came from my IAP member friends: Butternut from Rodney (Carpblaster), Lacewood and Wenge from Jeremy (Glycerine), and Rosewood from Eric (Buzz4). The aluminum sheets are also from my friend Rodney that he sent to me when we did the Transformation Swap. I provided the kit and the black pickguard that I ordered special to try out on this project.
I wanted to make a patchwork style pen with the wood grains running in multiple directions. I also wanted metal between every piece of wood. I drew a rough picture of my idea and started cutting and gluing the wood at varying angles one piece at a time. For my next one, I need to have a better way to make each adjoining surface come out perfectly flat, but all in all, it came out pretty good. I used medium CA for the glue. Here is how the blank ended up before I spliced in the pickguard.
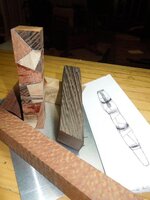
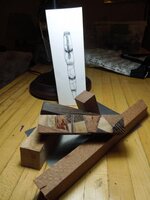
My original design was to have the black pickguard running in the same direction/angle on both barrels. Here are the two barrels with the pickguard.
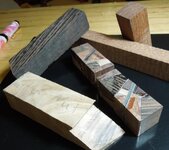
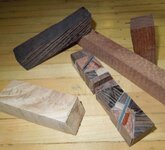
In my reading on the IAP forum, I have learned that there is a likelihood of blowouts occurring doing the drilling step on segmented pens. I've seen that a preventive technique for that is to glue on popsicle sticks or wrap the blanks in tape or string (and then soak the string with CA)... I thought that I would go further and I glued on paint sticks. Unfortunately, the paint sticks made the blanks too thick and they would not fit properly into my drill press centering jig. I had to mount them differently and use a square and my eyeballs to line it all up and hope for the best. One came out almost perfect and the other was close. Here's a pic of the glued-up-paint-sticked blanks. And here is my first 'teaser pic' that I sent to Russ! That was really fun because he then sent me a teaser pic of the wood that he was to use in his pen to me. He challenged me, but I could not guess what it was!
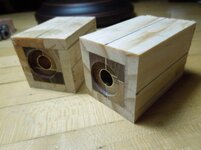
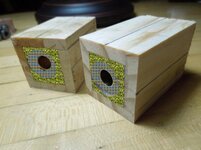
Due to general life schedules…, a long time went by before I could turn the blanks. I was pretty nervous about blowing them up because I didn't think that I would have time to make another set. For the most part, they turned just fine. I kept my tool sharp and took my time. I also practiced with the CA finish along the way (something else that I learned from IAP). I haven't been very successful with CA finishes, but I was determined to make it work this time! Here are a couple of pics of turning off the paint sticks…
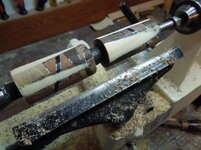
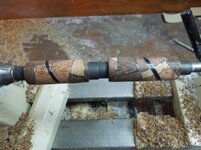
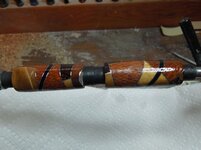
and my second set of 'teaser pics' that I sent to Russ.
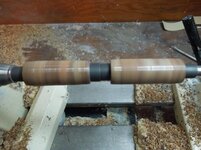
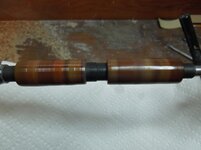
And then, of course when I'm close to done, I caught some metal glued onto a very tiny piece of wood right at the top end of the pen.I don't know where that piece flew off to, but I quickly started on the repair. I glued on a new piece of metal and a replacement piece of wood. At least this could be hidden under the clip!!
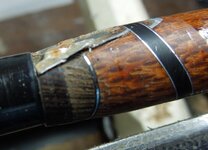
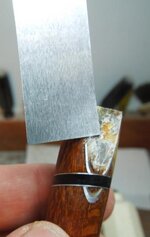
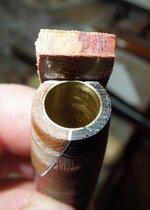
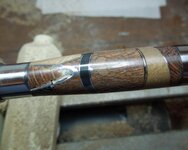
The finishing went very well! I took my time and applied it thin, but a lot of coats. I had been experimenting using the parts baggies over my fingers, and it was working better for me than using paper towels, but I still wasn't getting the finish that I see so many others getting. I constantly struggle with trying not to get ridges and dull spots. This time I used very small pieces of paper towel, just two layers thick, and the parts baggies over my finger. I think it helped me because I could feel it better like when it was just baggie, but I still had a little bit of towel to help control the amount being spread. I'm going to try this method again next time. I did have a tough time getting one of the bushings off and you can tell where that occurred if you study the pen. Next time I'm having trouble like that, I think that I will have to put it aside for awhile and make sure it is fully cured, take more time and go slow and easy (and hope).
One other imperfection about this one is that the Wenge has little pits in places. I think that the CA did fill the little holes, but since it is so clear, it did not make them disappear. They are quite little, but you can definitely still see them.
Assembling went easy. I've made lots of these cigar pens. My original design changed to make the pickguard angles in opposite directions instead of parallel. I needed to hide the repair job under the clip :redface: and the look flows just fine with the change


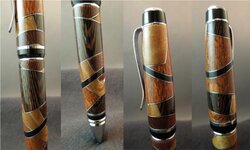
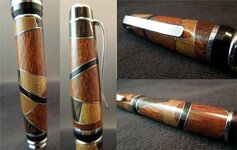
I included in my package to Russ as many blanks as I could fit in the box. I know he likes the Australian woods so I found a few of them, but I also wanted to put some stuff that he may not have done before. I have a pretty good supply of Dymondwood, so I added some different colors of it. He hasn't done any acrylics yet, so I put a couple of them in there with some other non-wood blanks - a good array of something different to complete the box stuffing. Merry Christmas Russ!

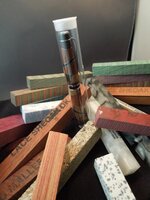
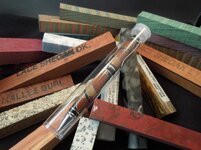
So, as with my other new-to-me techniques/kinds of pens that I spent a lot of time on and overcoming obstacles along the way, I wanted to share my story about this one. What made it even more fun was the PITH exchange part of it and getting to know my new friend Russ!
I hope that you like it and thanks for reading!
Greg
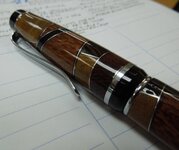