Texatdurango
Member
Quite a few members are posting their kitless creations but few are adding clips and I know why.... you think it's too hard!
Well, it's not really and to prove it, here is one way I do my clips. There are a number of tutorials in the library showing different methods but none show this way (I don't think) so here is a brief explanation and a few photos.
I use black finials that screw into the cap. I choose black because I like the contrast and they match the lower black finials as well and nothing looks sharper than a glossy black finial!
First I decide on the diameter of the caps I want then make my finials a handful at a time. I turn the tenons and cut the threads to where every finial is exactly the same and are all interchangeable. I personally chose 9mm x .75 threads which allow my chosen clip rings to fit snugly around the threads.
I chuck a round blank in my collet chuck and drill a "Q" hole all the way through. On the top end I use a 9mm x .75mm tap and thread the "Q" hole to allow the finial to screw in. I measure the diameter of the clip ring then cut the same diameter slot in the cap so the clip fits snugly when the finial is screwed on. Then it's just a matter of cutting a slot for the clip to sit in.
Not trying to convince anyone in changing their ways, this is just another way and is very quick and simple!
Well, it's not really and to prove it, here is one way I do my clips. There are a number of tutorials in the library showing different methods but none show this way (I don't think) so here is a brief explanation and a few photos.
I use black finials that screw into the cap. I choose black because I like the contrast and they match the lower black finials as well and nothing looks sharper than a glossy black finial!
First I decide on the diameter of the caps I want then make my finials a handful at a time. I turn the tenons and cut the threads to where every finial is exactly the same and are all interchangeable. I personally chose 9mm x .75 threads which allow my chosen clip rings to fit snugly around the threads.
I chuck a round blank in my collet chuck and drill a "Q" hole all the way through. On the top end I use a 9mm x .75mm tap and thread the "Q" hole to allow the finial to screw in. I measure the diameter of the clip ring then cut the same diameter slot in the cap so the clip fits snugly when the finial is screwed on. Then it's just a matter of cutting a slot for the clip to sit in.
Not trying to convince anyone in changing their ways, this is just another way and is very quick and simple!
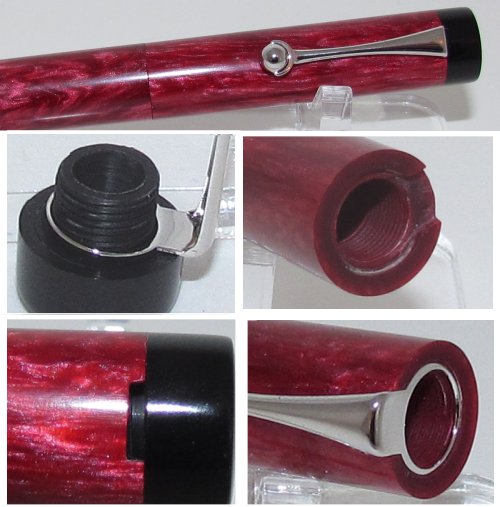
Last edited: