Timbo
Member
I glued up some blanks made of 4 woods, one of them being Walnut which is much softer than the other woods. Turns out when you drill it, the bit go off-center toward the softer Walnut. Yes...my bits are sharp. I'm drilling on my lathe, upping the speed helps, but it does not eliminate the problem completely. I'm hoping that stabilization will get the Walnut closer in hardness to the other woods and eliminate the problem.
I'm not quite ready to buy a stabilization system, so I'm looking for someone who stabilizes with cactus juice to run 7 blanks through their system for me. Can pay with cash or blanks. Please PM me if you can help me out, and what you want in payment. Thanks.
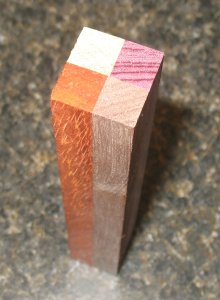
I'm not quite ready to buy a stabilization system, so I'm looking for someone who stabilizes with cactus juice to run 7 blanks through their system for me. Can pay with cash or blanks. Please PM me if you can help me out, and what you want in payment. Thanks.
Last edited: