ChrisN
Member
This was supposed to be a glorious tale about how easy it is for an inexperienced, yet inspired turner to enter the hallowed halls of custom pen making. Well, let's just say that has yet to happen....
So, I finally collected all the paraphernalia I needed to make a section. Drill bits, taps, dies, nibs, material - all here at last! Diligently taking notes, I proceeded to destroy several mm's of my clear acrylic attempting to make a tenon. At last, I ended up with a tenon that suited me. Loading my custom die holder (inspired by Texatdurango's) with my die; and dousing the section, die, lathe, workbench, and wall with Pam; I proceeded to thread the tenon without incident.
Next step was to drill a hole the whole way through. That also proceeded without incident (except for more Pam on the section, lathe, wall, etc.). Using my 6.4mm drill bit, I then drilled a second hole for the slip-fit joint between section and converter.
Now, time to turn it around!
With diligent measuring, I determine how long to make my section. Threading the section into a Delrin holder, I grabbed my 1/16" parting tool and went to work. Alas, that was the wrong thing to do! After the section, minus the tenon, landed on the floor; I realized I should have rough-cut it to length on my bandsaw. Well, another thing for the notes, I guess.
Hurriedly redoing the tenon, I had a little mess-up with the threads. Oh well, just 1mm of threads or lack of them on the end of the tenon won't hurt.
So, now we're back to the rough cutting step. This time, I do it on the bandsaw and just do touch-up on the lathe. After 3 more holes, and a tap, the section was complete! Time for a test-fit.
Hmm, the feed goes in a bit hard. Maybe I ought to re-think a few of those drill bit sizes. But, so far so good. Now time for the converter. It slips in very nicely, but doesn't really latch on to the feed! So I measure a bit and discover I didn't measure enough. The section was about 2mm too long! OK, I'll just take it apart and trim it down. But wait, the feed sleeve, due to the too tight hole sizes, is stuck!
I take it back to the lathe, and very delicately start trimming the section down with the sleeve of the feed still inside. Fortunately, the 2mm I had to trim off allows just enough of the sleeve for me to grasp it tight enough to turn it out.
Re-drilling the holes, with bit sizes a hair larger than the last time, progressed without a problem. Now, back to the test-fit again! Hmm, still too tight. Back to the lathe. Drill with a bit that's a bit larger than the last time. Test-fit. Success! Nib goes in nicely. Converter fits nicely. Notes taken nicely. YAAAAAAAAAAYYYYYYYYYYYYYYY!
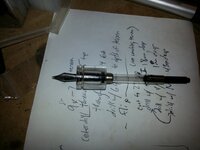
Now, just the shaping remains. Back to the lathe with the section I go. Well, you can about guess what happens next. GRRRRRRRRRRRRRRRRRRR!
I think I'll retrieve the piece from the trash. It will be a good practice piece for polishing inside holes.....
Well, at least I have all the steps for making a section written down. Next time it shouldn't take as long. It was intended to be a practice piece anyway.... Until next time!
(PS: If you didn't guess, the tenon broke off)!
So, I finally collected all the paraphernalia I needed to make a section. Drill bits, taps, dies, nibs, material - all here at last! Diligently taking notes, I proceeded to destroy several mm's of my clear acrylic attempting to make a tenon. At last, I ended up with a tenon that suited me. Loading my custom die holder (inspired by Texatdurango's) with my die; and dousing the section, die, lathe, workbench, and wall with Pam; I proceeded to thread the tenon without incident.
Next step was to drill a hole the whole way through. That also proceeded without incident (except for more Pam on the section, lathe, wall, etc.). Using my 6.4mm drill bit, I then drilled a second hole for the slip-fit joint between section and converter.
Now, time to turn it around!
With diligent measuring, I determine how long to make my section. Threading the section into a Delrin holder, I grabbed my 1/16" parting tool and went to work. Alas, that was the wrong thing to do! After the section, minus the tenon, landed on the floor; I realized I should have rough-cut it to length on my bandsaw. Well, another thing for the notes, I guess.
Hurriedly redoing the tenon, I had a little mess-up with the threads. Oh well, just 1mm of threads or lack of them on the end of the tenon won't hurt.
So, now we're back to the rough cutting step. This time, I do it on the bandsaw and just do touch-up on the lathe. After 3 more holes, and a tap, the section was complete! Time for a test-fit.
Hmm, the feed goes in a bit hard. Maybe I ought to re-think a few of those drill bit sizes. But, so far so good. Now time for the converter. It slips in very nicely, but doesn't really latch on to the feed! So I measure a bit and discover I didn't measure enough. The section was about 2mm too long! OK, I'll just take it apart and trim it down. But wait, the feed sleeve, due to the too tight hole sizes, is stuck!
I take it back to the lathe, and very delicately start trimming the section down with the sleeve of the feed still inside. Fortunately, the 2mm I had to trim off allows just enough of the sleeve for me to grasp it tight enough to turn it out.
Re-drilling the holes, with bit sizes a hair larger than the last time, progressed without a problem. Now, back to the test-fit again! Hmm, still too tight. Back to the lathe. Drill with a bit that's a bit larger than the last time. Test-fit. Success! Nib goes in nicely. Converter fits nicely. Notes taken nicely. YAAAAAAAAAAYYYYYYYYYYYYYYY!
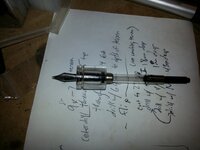
Now, just the shaping remains. Back to the lathe with the section I go. Well, you can about guess what happens next. GRRRRRRRRRRRRRRRRRRR!
I think I'll retrieve the piece from the trash. It will be a good practice piece for polishing inside holes.....
Well, at least I have all the steps for making a section written down. Next time it shouldn't take as long. It was intended to be a practice piece anyway.... Until next time!
(PS: If you didn't guess, the tenon broke off)!