Brandon25
Member
I've been fine using a pistol grip clamp for my pens thus far, but I've got about twenty slimlines to assemble soon, and I get very nervous assembling the tip. This is the only place I've ever had a blank crack on me during assembly, and it's happened numerous times. Pretty sure the cause is the tip being pressed in a little crooked, which for me at least is hard to prevent using the clamp as my press. Even when I hold the parts with one hand, it's hard to keep the tip lined up at that critical moment when the fitting enters the brass tube.
Long story short, I happened upon a $5 horizontal toggle clamp today rated at 500 pounds, so I want to try to make a pen press. I have a few questions- do you guys who have made or tried several find that the inserts that shorten the capacity to your desired length work better than, say, woodcraft's adjustable shaft with locking nut? Also, when making the part opposite the toggle clamp, should the contact point that touches the pen be straight, or have a hole, or be turned with a conical recess similar in size to my slimlines? I dont just do slimlines though, so I'm not sure if a straight-walled hole might be better. Would a straight walled hole really even help much for keeping my pen tip straight when pressing?
Sorry for the long post and numerous questions, but I wanna get this right the first time, else my savings over a store-bought model will dwindle with my wasted time increase.
Here's the idea I drew up in MS Paint.
Long story short, I happened upon a $5 horizontal toggle clamp today rated at 500 pounds, so I want to try to make a pen press. I have a few questions- do you guys who have made or tried several find that the inserts that shorten the capacity to your desired length work better than, say, woodcraft's adjustable shaft with locking nut? Also, when making the part opposite the toggle clamp, should the contact point that touches the pen be straight, or have a hole, or be turned with a conical recess similar in size to my slimlines? I dont just do slimlines though, so I'm not sure if a straight-walled hole might be better. Would a straight walled hole really even help much for keeping my pen tip straight when pressing?
Sorry for the long post and numerous questions, but I wanna get this right the first time, else my savings over a store-bought model will dwindle with my wasted time increase.
Here's the idea I drew up in MS Paint.
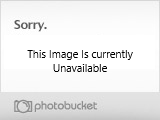