jleiwig
Member
Is this feasible or am I just being crazy? I saw something similar in an article by david reed smith.
A 2 jaw chuck for drilling call blanks on the lathe. I don't have the money right now for a real chuck or drill press, so I thought this idea up last night. It wouldn't take long to whip it up, and I could be drilling my call blanks and practicing making calls
Here is the base. A 4" Dia. 1" thick piece of hardwood screwed to a faceplate with two grooves routed in it to hold pieces of t-track.
Here are the jaws. 2 pieces of 3.5" dia hardwood 2" thick with a square hole cut out in the middle that is just slighly smaller than 1 1/2" square. I think I will make one side non-moveable and the otherside moveable with some adjuster knobs. Just have to make sure I get them centered so I can drill centered.
Since this is only for drilling I think it would work. What say you?
A 2 jaw chuck for drilling call blanks on the lathe. I don't have the money right now for a real chuck or drill press, so I thought this idea up last night. It wouldn't take long to whip it up, and I could be drilling my call blanks and practicing making calls
Here is the base. A 4" Dia. 1" thick piece of hardwood screwed to a faceplate with two grooves routed in it to hold pieces of t-track.
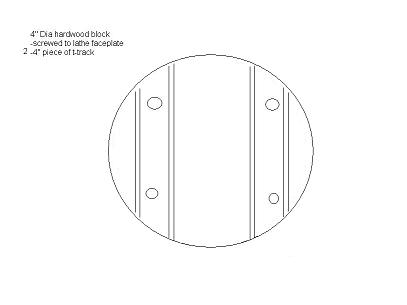
Here are the jaws. 2 pieces of 3.5" dia hardwood 2" thick with a square hole cut out in the middle that is just slighly smaller than 1 1/2" square. I think I will make one side non-moveable and the otherside moveable with some adjuster knobs. Just have to make sure I get them centered so I can drill centered.
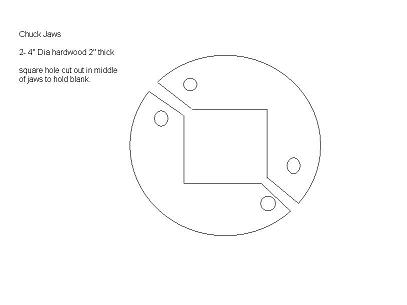
Since this is only for drilling I think it would work. What say you?