Hello,
I'm new to wood turning and have finished 3 or 4 kits so far. I have already had 3 blanks 'explode' on me on the lathe. The first, a piece of figured walnut, second one was a piece of cocobolo, and another piece of walnut again this evening. This is getting frustrating!
The first two were assembled with CA, and it looked like part of the problem at least was due to incomplete glue coverage. I switched to epoxy on my latest ones, thinking it would solve that problem, but it doesn't seem to have. I am applying plenty of excess glue, it is oozing out as I spin it slowly to insert it.
Is there a trick to getting complete glue contact? Is this part/all of the problem, or is it something else that I'm doing wrong?
Thanks!
Here is a photo of the first one (walnut/CA)...I will try to take a shot of the epoxied one to post tomorrow.
I'm new to wood turning and have finished 3 or 4 kits so far. I have already had 3 blanks 'explode' on me on the lathe. The first, a piece of figured walnut, second one was a piece of cocobolo, and another piece of walnut again this evening. This is getting frustrating!
The first two were assembled with CA, and it looked like part of the problem at least was due to incomplete glue coverage. I switched to epoxy on my latest ones, thinking it would solve that problem, but it doesn't seem to have. I am applying plenty of excess glue, it is oozing out as I spin it slowly to insert it.
Is there a trick to getting complete glue contact? Is this part/all of the problem, or is it something else that I'm doing wrong?
Thanks!
Here is a photo of the first one (walnut/CA)...I will try to take a shot of the epoxied one to post tomorrow.
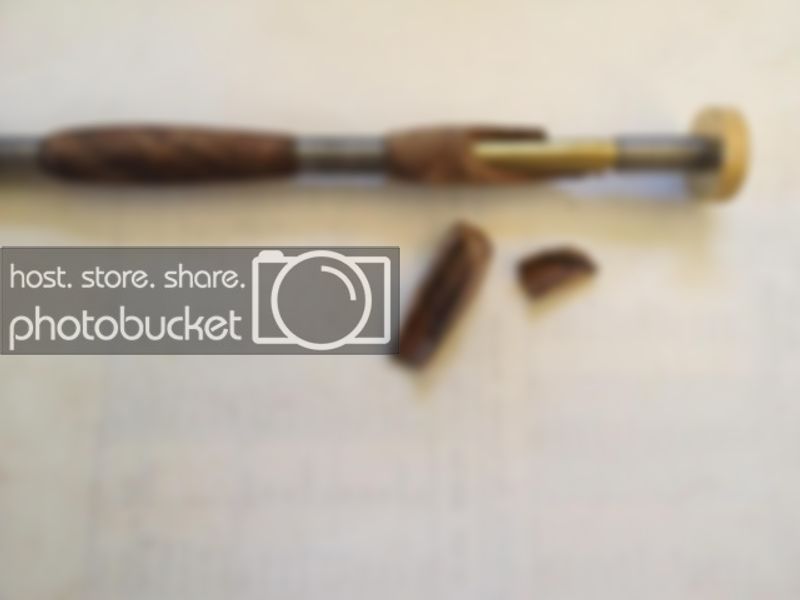