jimbob91577
Member
- Joined
- Aug 18, 2008
- Messages
- 280
So I have an idea, and it may have already been built, but my uncle does metal fabrication and I've asked him if he would build something for me. Before I have him do it though, I thought I would ask the folks on the forum for their input.
Basically, I'm looking for a closed end pen mandrel. I'd like something that is flexible enough to be used for multiple kit designs - thus I'm thinking of something like what is pictured below. It consists of a mandrel system and a sleeve. The sleeve, depicted below the mandrel system, will fit over the mandrel, following the appropriate bushing, and be secured by "O"-Rings and set screws. The pen barrel will fit over the sleeve and be secured by "O"-Rings. The Mandrel depth can be controlled by the two nuts on each end of the taper.
My question(s) are as follows:
- Will the taper work itself loose not having any pressure keeping it in the head of the lathe?
- Any problems with using "O"-Rings to secure a pen barrel to the sleeve?
- Any problems with the overall design?
Thanks!
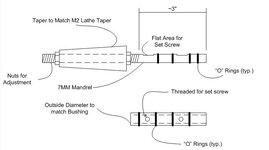
Basically, I'm looking for a closed end pen mandrel. I'd like something that is flexible enough to be used for multiple kit designs - thus I'm thinking of something like what is pictured below. It consists of a mandrel system and a sleeve. The sleeve, depicted below the mandrel system, will fit over the mandrel, following the appropriate bushing, and be secured by "O"-Rings and set screws. The pen barrel will fit over the sleeve and be secured by "O"-Rings. The Mandrel depth can be controlled by the two nuts on each end of the taper.
My question(s) are as follows:
- Will the taper work itself loose not having any pressure keeping it in the head of the lathe?
- Any problems with using "O"-Rings to secure a pen barrel to the sleeve?
- Any problems with the overall design?
Thanks!
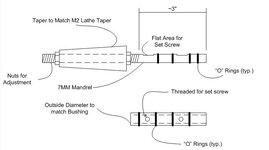