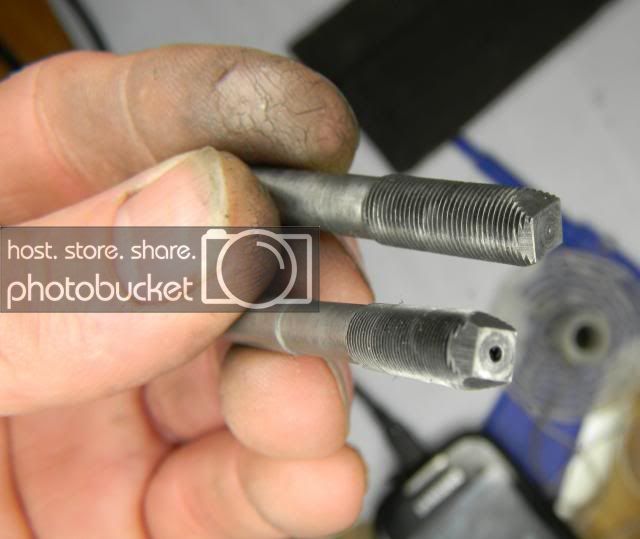
Tap to suit a #6 Bock triplet Below tap to suit a Schmidt 6.4x0.4
My guess this method has been posted in the past.
I once worked in a tool room where we had to make our own taps for those *propitiatory *(commonly known as bastard threads.)
You can use water hardened drill rod or oil hardened drill rod.
I used water hardened as thats all I have on my steel rack.
With such fine threads we use for fountain pens accurate machining is required as a few thou. can make a lot of difference.
1-2 thou. over the major dia. of the thread or improper form to the thread can result in an unusable tap.
You also have to make allowance for expansion and contraction during hardening and annealing.
Where only talking about 0.4 p or 0.016 thou depth of thread so care must be taken and constant checking with the loupe to see how the threads are forming whilst being screw cut
Turning between centers is critical as any flexing of the work piece can result in the work ending up in the bin.
I used a single pointed tool to cut the threads then a thread chaser to form the threads properly at the root diameter.
The section behind the thread is then turned down to 1-2 thou below the tapping drill size....this aids in remembering what drill is to use for taping
Finally the flutes are ground or filed on to the cutting point.
An old tradey showed me this method back in my apprenticeship days.
Two opposing sides should be deeper than the opposing sides forming a rectangle at the point.
This is enough fluting to clear the chips.....but should be cleared constantly to avoid clogging.
The hardening process is quite simple. Heat to a cherry red.
and then quench the tap in a bucket of *water. *(This is also the point where the work piece is no longer magnetic.)
I then clean the threads with a small wire brush disk on a Dremal tool.
This is so it is no longer black from quenching but shinny.
Lastly the item needs to be annealed because after hardening the tap is very hard but also very brittle.
Reheat the item starting at the opposite end so the heat runs towards the important part of the work piece threads and when it gets to the dull straw colour its time to STOP and let it cool down.
If it does start to turn dark straw or blue keep heating it up and start back at the beginning.
I used my home made LPG stove to get the cherry red as my oxy cylinder is empty then a LPG torch for the annealing.
I do hate it when you make a tap and it just not quite right...and you have to start again.
However the process can be reversed by heating the item back up to cherry red and placing it in a bucket of lime for 6+ hours.
then it can be re-machined BTW: this works fantastically on steel balls if you want to drill or make a part with a knob or ball on it
Hope this might help someone!
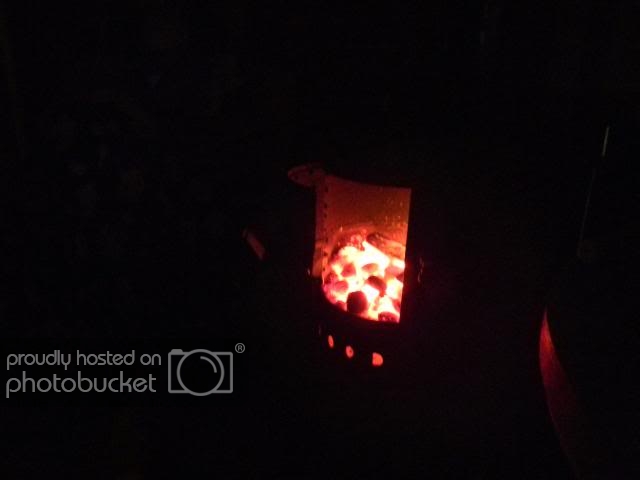