JD Combs Sr
Member
... of a leak.:redface: So guess what all my Alumilite mix ran out into the pressure pot.
I had every thing ready to go and was waiting for the weather to cool a little and it did.
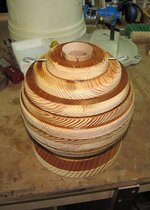
So I poured my mix and this is pretty much what it looked like after the pour, a minor amount of overflow. I let it set over night and removed the pressure lid and it looked liked this. I grabbed the two hooks to pull it out of the pot and oops, stuck like it was part of the pot. Using a flashlight I could barely see down the side of the vase and I thought I could see resin...hmmmm that shouldn't be, :frown:but it was. I spent the next hour beating on the side and bottom of the pot with a rubber mallet to see if I could knock anything loose, nada!
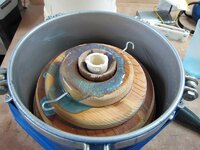
I finally gave up and decided that I need to do something different so I drilled a hole in the bottom and attached an air fitting. Cranked my air hose pressure down to 50lbs and attached it. Still nada!
Now I figure every thing is a loss including the pot so what the heck I cranked the pressure up to 80... nothing, so I just left it like that lying on the floor of the shop. About 15-20 minutes later I started hearing the hiss of escaping air. It was coming from the pot. I picked up the rubber mallet that was still handy and whacked the bottom sides a few times and all of a sudden the vase was sticking halfway out of the pot. Eureka, it worked.:biggrin:
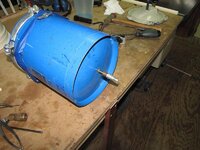
This is what it looked like after I finished prying it out of the pot. Anybody know what will melt Alumilite. I got to clean that pot up now.
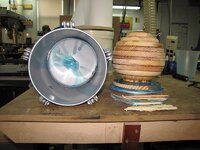
I had every thing ready to go and was waiting for the weather to cool a little and it did.
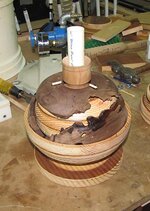
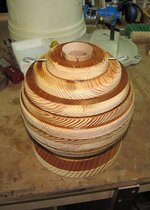
So I poured my mix and this is pretty much what it looked like after the pour, a minor amount of overflow. I let it set over night and removed the pressure lid and it looked liked this. I grabbed the two hooks to pull it out of the pot and oops, stuck like it was part of the pot. Using a flashlight I could barely see down the side of the vase and I thought I could see resin...hmmmm that shouldn't be, :frown:but it was. I spent the next hour beating on the side and bottom of the pot with a rubber mallet to see if I could knock anything loose, nada!
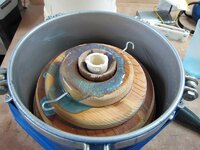
I finally gave up and decided that I need to do something different so I drilled a hole in the bottom and attached an air fitting. Cranked my air hose pressure down to 50lbs and attached it. Still nada!
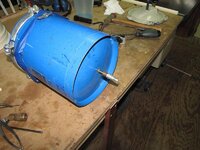
This is what it looked like after I finished prying it out of the pot. Anybody know what will melt Alumilite. I got to clean that pot up now.
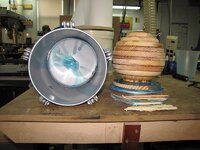
Last edited: