thewishman
Member
After a few issues with cracking blanks while pressing parts together, I tried a few things. The best way that I found was to reduce the inside diameter of the brass tube. (Sanding the male pen parts causes way to much risk of damaging the plating.)
Sure, a Dremel can do the job, but the wheels are expensive, and they need to be replaced often. I wanted a solution that I could repeat quickly and with a low cost.
Using a transfer punch and a small piece of Abranet (I'm using 120 grit, because that's what I have on hand) I can abrade enough of the brass to create a slip fit for the pen parts quickly. I mount it in a jacobs chuck.
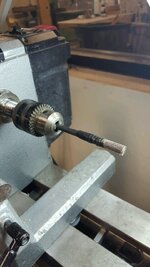
After testing the idea, the best way I have found is to take an inch wide strip of Abranet and taping the first 1/4" to the punch, wrapping it carefully in the direction it will spin. Wrap it around a couple of layers thick, I use electrical tape to attach it to the punch. Be careful that there is no overhang Abranet, make the end flush with the punch.
I found that having a couple of punches set up in different diameters can cover most of the pens I make. My next step is to get a second set of transfer punches and prepare a few sanders so I can quickly switch them out as the Abranet wears.
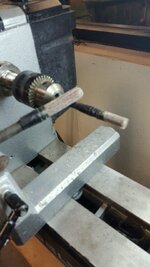
Sure, a Dremel can do the job, but the wheels are expensive, and they need to be replaced often. I wanted a solution that I could repeat quickly and with a low cost.
Using a transfer punch and a small piece of Abranet (I'm using 120 grit, because that's what I have on hand) I can abrade enough of the brass to create a slip fit for the pen parts quickly. I mount it in a jacobs chuck.
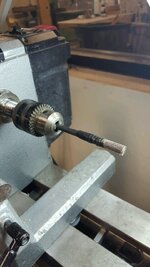
After testing the idea, the best way I have found is to take an inch wide strip of Abranet and taping the first 1/4" to the punch, wrapping it carefully in the direction it will spin. Wrap it around a couple of layers thick, I use electrical tape to attach it to the punch. Be careful that there is no overhang Abranet, make the end flush with the punch.
I found that having a couple of punches set up in different diameters can cover most of the pens I make. My next step is to get a second set of transfer punches and prepare a few sanders so I can quickly switch them out as the Abranet wears.
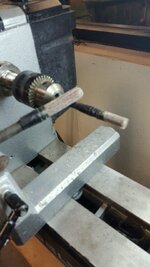