woodwzrd
Member
I bought a gallon of alumilite with the bash discount and just finally got a chance to cast some of it. So far I am 0 for 2. I am trying to cast some cholla blanks. Here is what is going on. I have a mold that I made out of cutting board just like the stuff Curtis uses. The first run I cut my cholla to fit in my mold. I then mixed the resin by weighing out 4.5 oz of the A side. Next I added my pearl exe and mixed it in really good. Lastly I added 4.5 oz of the B side to the tinted A side and mixed it for about 30-45 seconds. Then I put them in the pressure tank at 80 lbs. for 2 hours. I did not use any kind of mold release. When I tried to de-mold the blanks they were stuck tight. I tried to pry them out with a screw driver and they broke a part. They kind of reminded me of what a piece of hard candy looks like after you drove it. There were areas where there was little if any bond with the cholla. I figured they stuck because I didn't use any mold release. Since I don't have any mold release, on round 2, I sprayed my mold lightly with a little WD 40. I did everything the same as in the first go around and got almost the same exact result only the second time around the blanks came out a little easier. They are still quite brittle with hit and miss bonding to the cholla. The only thing I can think of is it is too cold in my shop. When I case them it was just short of 50 degrees (latest heat wave). I am open to any suggestions as to what to do. I have an order for several of these blanks and would like to get them done soon but am stumped. The pic shows the blanks and what my mold looked like after I got the blanks out on the second attempt. Thanks for any help.
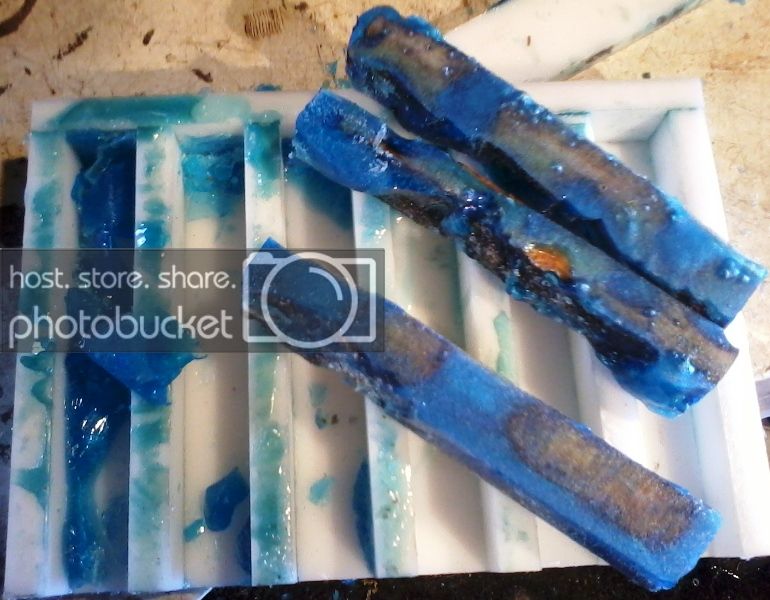