snowb46
Member
I'm having a blast....even without my lathe! Just ordered it on Thursday.
Just got a shipment yesterday of PC cane from Toni yesterday and spent a portion of the morning putting a PC blank together.
Still have the sanding to do yet, and had some questions for Toni about the process.
It's really fairly easy, just takes some time to to do. Here is what I've done so far:
CLICK on photo and will take you to the other pics on Photobucket
I'm looking forward to getting this down and making some more! Has anyone else done any of these?
Just got a shipment yesterday of PC cane from Toni yesterday and spent a portion of the morning putting a PC blank together.
Still have the sanding to do yet, and had some questions for Toni about the process.
It's really fairly easy, just takes some time to to do. Here is what I've done so far:
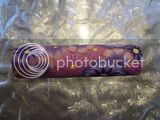
I'm looking forward to getting this down and making some more! Has anyone else done any of these?